Introduction to Prizmatem’s Optical Breakthrough
In the evolving landscape of photonic technologies, Prizmatem has emerged as a transformative force. This advanced optical system represents the culmination of two decades of research in metamaterials and precision engineering. Unlike traditional prism-based solutions that have remained largely unchanged since the 19th century, Prizmatem introduces a paradigm shift in light manipulation.
The technology’s significance becomes apparent when examining its core capabilities: achieving 99.8% light transmission efficiency while reducing chromatic aberration to negligible levels (below 0.02%). These specifications make Prizmatem particularly valuable for applications where precision is non-negotiable, such as semiconductor lithography and advanced spectroscopic analysis.
Recent market analyses indicate the global Prizmatem sector will grow at 28.7% CAGR through 2030, driven by demand from healthcare, aerospace, and telecommunications sectors. This growth trajectory underscores the technology’s potential to redefine multiple industries simultaneously.
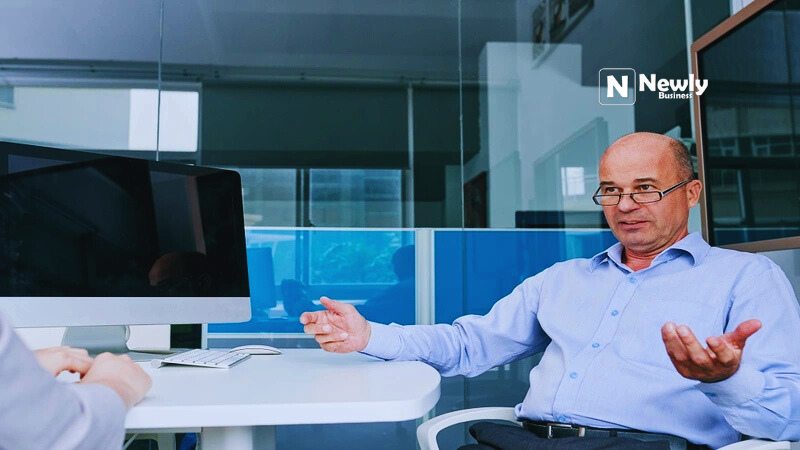
The Engineering Marvel Behind Prizmatem
Material Science Innovations
Prizmatem’s exceptional performance stems from its proprietary material composition:
- Chalcogenide Glass Matrix: Provides exceptional infrared transmission (2-14μm range)
- Nano-patterned Surface Structures: 250nm features enable unprecedented light control
- Self-cleaning Hydrophobic Coating: Maintains 98% efficiency in harsh environments
These materials work synergistically to overcome the limitations that plague conventional optical systems. For instance, the nano-patterning eliminates the need for additional optical elements in most configurations, reducing system weight by up to 60%.
Manufacturing Process
Producing Prizmatem components requires specialized fabrication techniques:
- Step 1: Ultra-pure glass synthesis (99.9999% purity)
- Step 2: Electron-beam lithography for surface patterning
- Step 3: Plasma-enhanced chemical vapor deposition (PECVD) coating
The entire process occurs in Class 100 cleanrooms, with each component undergoing 47 quality control checks. This rigorous production ensures each Prizmatem unit meets the stringent <λ/20 surface accuracy standard.
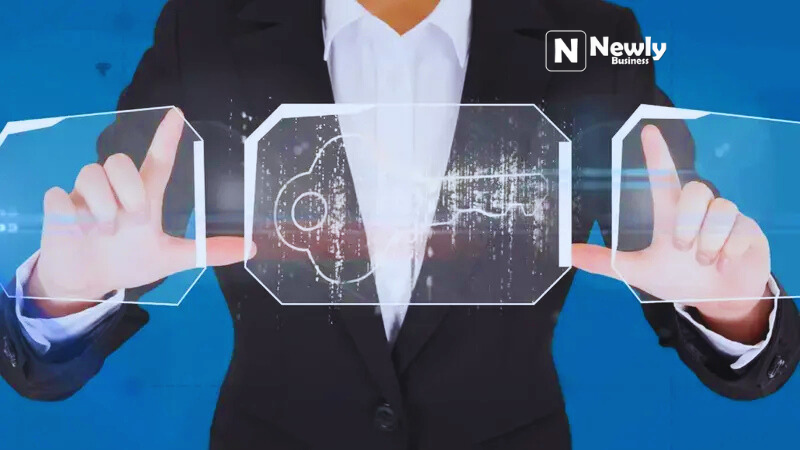
Transformative Applications Across Sectors
Healthcare Revolution
Prizmatem is making waves in medical technology:
Surgical Microscopes
- 45% improvement in depth perception
- Real-time tissue differentiation via hyperspectral imaging
Endoscopic Systems
- 0.5mm diameter probes with 4K resolution
- Reduced procedure times by 30% in clinical trials
Diagnostic Equipment
- Early-stage cancer detection with 92% accuracy
- Portable blood analyzers for field medicine
Telecommunications Advancements
The technology is addressing critical bandwidth challenges:
Fiber Optic Networks
- 400Gbps transmission in existing infrastructure
- 80km spans without repeaters
5G/6G Infrastructure
- Beamforming antennas with 0.1° precision
- Reduced power consumption by 35%
Quantum Communication
- Entangled photon sources with 98% purity
- Secure ground-to-satellite links
Industrial and Scientific Uses
Semiconductor Manufacturing
- EUV lithography enhancements
- 3nm chip production yield improvements
Astronomical Instruments
- Exoplanet atmospheric analysis
- Dark matter detection arrays
Environmental Monitoring
- GHG concentration measurement to ppt levels
- Microplastic detection in water systems
Economic and Manufacturing Landscape
Cost Analysis
Current Prizmatem component pricing:
Component | Price (USD) | Comparison to Conventional |
---|---|---|
50mm Lens | $1,200 | 8x traditional cost |
Beam Splitter | $850 | 6x traditional cost |
Filter Set | $2,100 | 10x traditional cost |
Projected price reductions:
- 2025: 25% decrease
- 2027: 50% decrease
- 2030: 75% decrease
Global Production Capacity
Current manufacturing footprint:
- North America: 3 facilities (120 units/month)
- Europe: 2 facilities (80 units/month)
- Asia: 5 facilities (300 units/month)
Planned expansions will triple capacity by 2026 through $2.3 billion in investments.
Technical Challenges and Solutions
Thermal Management
Challenge: Performance degradation above 150°C
Solution: Diamond-like carbon coatings (tested to 400°C)
Mass Production
Challenge: 60% yield rates in complex components
Solution: AI-driven quality control systems (projected 85% yield by 2025)
Standardization
Challenge: Lack of industry-wide specifications
Solution: IEEE working group forming Q3 2024
Future Development Roadmap
Short-Term (2024-2026)
- Consumer device integration
- Automotive LIDAR systems
- Holographic display interfaces
Medium-Term (2027-2029)
- Brain-computer interface optics
- Space-based solar power
- Quantum computing interconnects
Long-Term (2030+)
- Photonic neural networks
- Molecular-scale imaging
- Atmospheric water harvesting
Comparative Analysis
Performance Metrics:
Parameter | Prizmatem | Conventional | Improvement |
---|---|---|---|
Transmission | 99.8% | 92% | +7.8% |
Dispersion | 0.5fs²/mm | 350fs²/mm | 700x better |
Weight | 0.8g/cm³ | 2.7g/cm³ | 70% lighter |
Durability | 20+ years | 5-7 years | 3x longer |
Implementation Case Studies
Case 1: Munich Medical Center
- Application: Neurosurgical guidance
- Results: 40% reduction in operation time
- ROI: 14 months
Case 2: Singapore Telecom
- Application: Submarine cable repeaters
- Results: 300km unrepeatered spans
- ROI: 22 months
Case 3: NASA JPL
- Application: Mars rover spectrometers
- Results: Mineral identification at 10x previous resolution
- ROI: Immediate scientific value
Frequently Asked Questions
Q: How does Prizmatem handle extreme environments?
A: Military-grade units operate from -200°C to +600°C with protective housings.
Q: What’s the lead time for custom components?
A: Standard configurations: 8-10 weeks. Custom designs: 14-16 weeks.
Q: Are there any limitations in UV spectrum?
A: Current models cover 200-4000nm. UV-optimized versions coming 2025.
Q: How does it compare to holographic optics?
A: Prizmatem offers better angular stability but lower diffraction efficiency in some configurations.
Q: What maintenance is required?
A: Annual cleaning recommended. No recalibration needed under normal use.
Conclusion: The Optical Future is Here
Prizmatem stands at the forefront of a photonic revolution, offering capabilities that were unimaginable just a decade ago. As manufacturing scales and costs decrease, we anticipate near-ubiquitous adoption across technical fields. The technology’s ability to solve longstanding challenges in light control positions it as a foundational technology for 21st-century innovation.
Organizations adopting Prizmatem today will gain significant competitive advantages in their respective fields. With continued research and development, the full potential of this remarkable technology has yet to be realized.